5 April 2018
Let’s talk poop and how laboratory assistants at Shropshire’s two acute hospitals are improving the accuracy of C. diff test results.
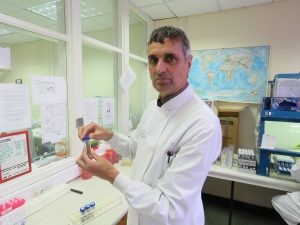
Alan Jackson holds a sample
You might want to go ‘ewww’ and wonder what kind of people talk about this stuff in polite company, but a team of white coats from the Royal Shrewsbury Hospital and Telford’s Princess Royal Hospital have put potty talk to good use to reduce the number of inaccurate Clostridium difficile (C. diff) results at The Shrewsbury and Telford Hospital NHS Trust (SaTH).
Such frank discussions, prompted by the improvement work SaTH are doing through its partnership with the Virginia Mason Institute in Seattle, has resulted in defects in C. diff being reduced by 13 per cent in just one month.
Alan Jackson, SaTH’s Head Biomedical Scientist for Cellular Pathology and Microbiology, explains: “When stool samples are sent to the laboratories for C. diff screening the medical assistants would follow the doctors’ orders and make sure every sample was tested.
“However, on closer examination, we found that 15 of the 78 requests sent to us in one chosen week should not have been sent for testing because they were not unformed stools. When screening for C. diff you should not test solid stools as it can lead to erroneous results.”
C. diff is a bacterium that can infect the bowel and cause diarrhoea. The infection most commonly affects people who have recently been treated with antibiotics, but can spread easily to others. The infection is unpleasant and can sometimes cause serious bowel problems, but they can usually be treated with another course of antibiotics.
Incorrect C. diff results, while unlikely due to follow-up tests, can result in unkind patient care, while the time wasted testing inappropriate samples could be better spent on other potentially life-saving procedures, not to mention a potential saving of approximately £13,000.
Mr Jackson, who conducted the mistake-proofing improvement work as part of his Advanced Lean Training, an intensive course that uses hands-on exercises to enable participants to deepen their lean learning and refine their skills and methods of a lean management system, worked with his team and found a way of improving the test – using a tool that resembles a turkey baster!
He said: “It’s a simple idea that barely costs us a penny, but by using a patette to draw the sample the team are able to quickly eliminate non-liquid stools because they won’t flow up the tube. It makes it easy to choose which samples to test and which ones to discard.
“One month later and only nine unnecessary tests were undertaken out of 142 over a two week period. That means defect tests have been reduced from 19.2% to just 6.2%.”
Staff who pass their Advanced Lean Training are considered to have a deep understanding of lean learning, as well as building the capacity to teach, coach and mentor others in the tools and methods of a lean management system.